
The Work Sharp E3-again, the nearest competitor in our test-doesn’t have an equivalent mechanism. But it adds a feature that others lack: spring-loaded guides inside the slots that grip the blade at the correct angle and keep it from shifting around during the sharpening process. Like most electric sharpeners, the Trizor XV uses rigid, angled slots to help orient the blade. When sharpening by any method, it’s critical to hold the blade at a consistent angle: If you don’t, the result is a rounded-over, dulled edge, rather than a sharp one formed by the apex of two consistent bevels. One reason the Trizor XV produces consistently sharp knives is its design, which makes it virtually impossible to mess up the sharpening process. (If you’re running the numbers and coming up short, bear in mind that resetting the blade for each pull, and intermittently testing the edge, adds considerably to the total time elapsed.) And on badly dulled knives, we sometimes ran to 30 pulls on the Work Sharp E3, which took about 8 minutes. The total number of pulls sometimes topped out lower, at around 20, but because every pull took about 8 seconds, when going by the instructions, the total time was greater. By contrast, on the Work Sharp E3, it took at least 5 minutes to sharpen an 8-inch knife, and often longer. Following the instructions, we found that every “pull” of an 8-inch blade through the sharpener took between 5 seconds (on the coarse abrasive) to just 1 or 2 seconds (on the fine “stropping/polishing” abrasive), and the total number of pulls topped out at around 30. From start to finish, it took us a maximum of 4 minutes to bring an 8-inch knife from a sandpaper-dulled state to a like-new edge. Elastic model systems can be used to enhance our understanding of biofilm physico-mechanics and their role in marine drag.And the Trizor XV sharpens knives fast. From statistical analysis it was confirmed that material mechanical properties, such as elasticity, and surface roughness both significantly affect drag. Pressure drop measurements, expressed as a friction coefficient, revealed that the elastomeric sandpaper replicas had a significantly higher associated drag, of up to 52%, when compared to the rigid counterparts. The marine biofilm flow cell was fitted with a clear lid, which allowed real-time visualisation of the replicas’ surface topography using Optical Coherence Tomography. Profilometry confirmed that there was no significant difference between the roughness of the rigid sandpaper sources and the material replicas. To control for roughness parameters and surface topography the replicas were created for sandpaper grit numbers: P40, P80 and P240 with average measured roughness (S a) of 108, 49 and 16 μm, respectively. Elastomeric sandpaper replicas were generated to be used as model systems for investigating the effect of roughness and elasticity on drag, over the Reynolds number range of approximately 2.0 × 10 4 to 5.2 × 10 4 Re using a marine biofilm flow cell.
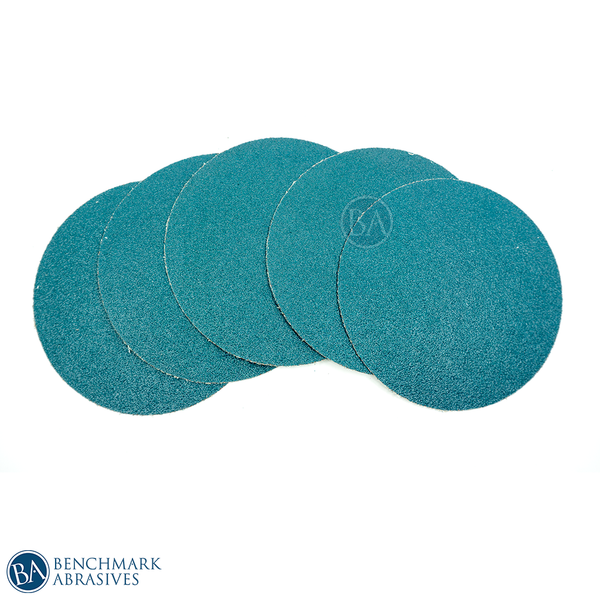

As a result, rigid structures are typically used as the benchmark for studying biofilm-associated drag.
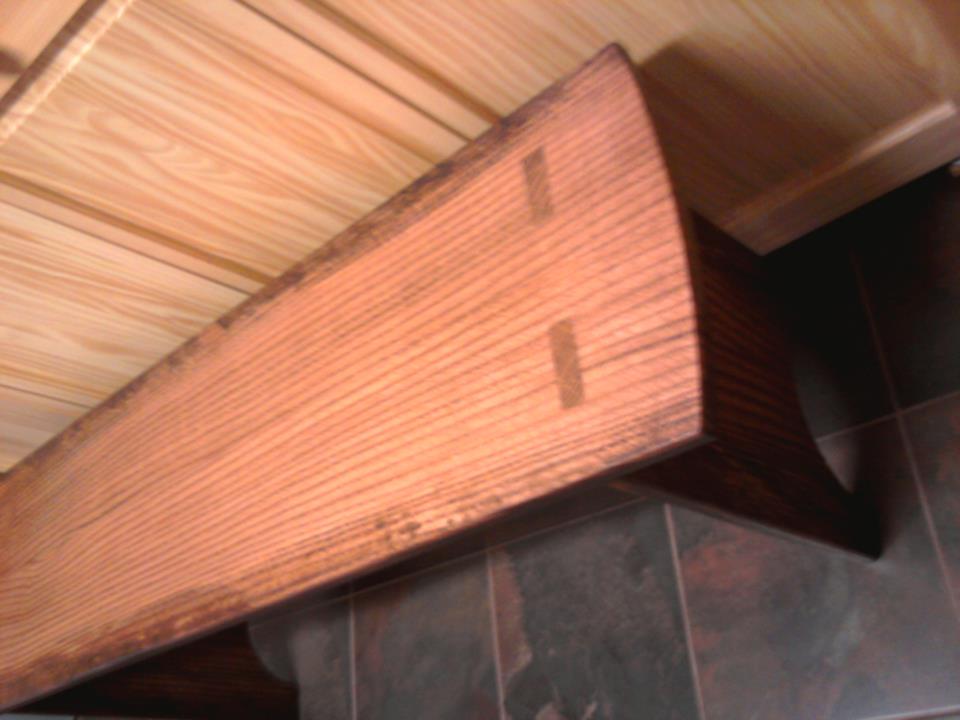
Biofilm heterogeneity and adaptability complicates efforts to link biofilm structural and mechanical properties to frictional drag.
